Beverage System Manufacturing
Transforming concepts into reality, our contract manufacturing services for the Electro-Mechanical Beverage Systems Industry blend precision engineering with cutting-edge technology for optimal performance and efficiency.
Beverage System Manufacturing
Transforming concepts into reality, our contract manufacturing services for the Electro-Mechanical Beverage Systems Industry blend precision engineering with cutting-edge technology for optimal performance and efficiency.
Beverage Manufacturing Solutions
At Providence Enterprise, we understand the pivotal role of consumer and commercial beverage dispensing systems in your business. Delays or malfunctions can lead to customer dissatisfaction and revenue loss.
Our commitment is to provide reliable, innovative solutions tailored to your needs, ensuring seamless operation and customer satisfaction.
Quality and Compliance
Achieve precision, reliability, and compliance with our stringent quality control systems. Partner with us for safe, effective beverage and smart system solutions that elevate your product's reputation and ensure market readiness.
Accelerated Time to Market
Collaborate with us for swift and efficient manufacturing of consumer and commercial beverage dispensing systems. Our expert team ensures rapid delivery of high-quality products, providing you with a competitive edge and enhancing customer satisfaction.
Cost-Effective Scalability
Drive profitability with cost-effective production solutions tailored for the beverage dispensing systems industry. Benefit from our expertise in resource management and economies of scale, ensuring efficient scaling and reduced manufacturing costs specifically for consumer and commercial beverage dispensing systems.
Beverage Manufacturing Solutions
At Providence Enterprise, we understand the pivotal role of consumer and commercial beverage dispensing systems in your business. Delays or malfunctions can lead to customer dissatisfaction and revenue loss.
Our commitment is to provide reliable, innovative solutions tailored to your needs, ensuring seamless operation and customer satisfaction.
Quality and Compliance
Achieve precision, reliability, and compliance with our stringent quality control systems. Partner with us for safe, effective beverage and smart system solutions that elevate your product's reputation and ensure market readiness.
Accelerated Time to Market
Collaborate with us for swift and efficient manufacturing of consumer and commercial beverage dispensing systems. Our expert team ensures rapid delivery of high-quality products, providing you with a competitive edge and enhancing customer satisfaction.
Cost-Effective Scalability
Drive profitability with cost-effective production solutions tailored for the beverage dispensing systems industry. Benefit from our expertise in resource management and economies of scale, ensuring efficient scaling and reduced manufacturing costs specifically for consumer and commercial beverage dispensing systems.
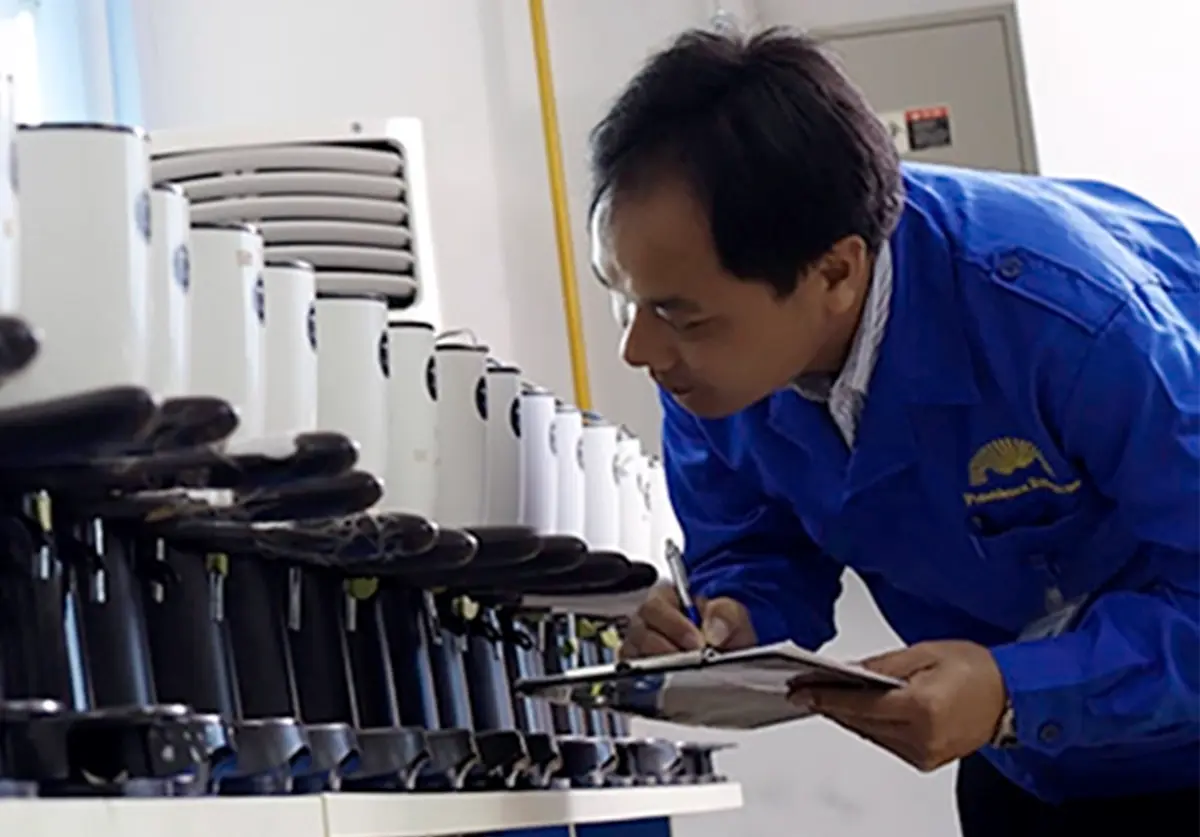
Beverage System Innovation
We're your go-to partner for developing and manufacturing beverage systems, turning your ideas into reality with quality and innovation.
View Detailed List
- Consumer & Commercial Systems: Food, Espresso, Coffee, Tea, & Water Appliances
- Connected Systems: WiFi, Bluetooth, Zigbee, Z-Wave, and RFID
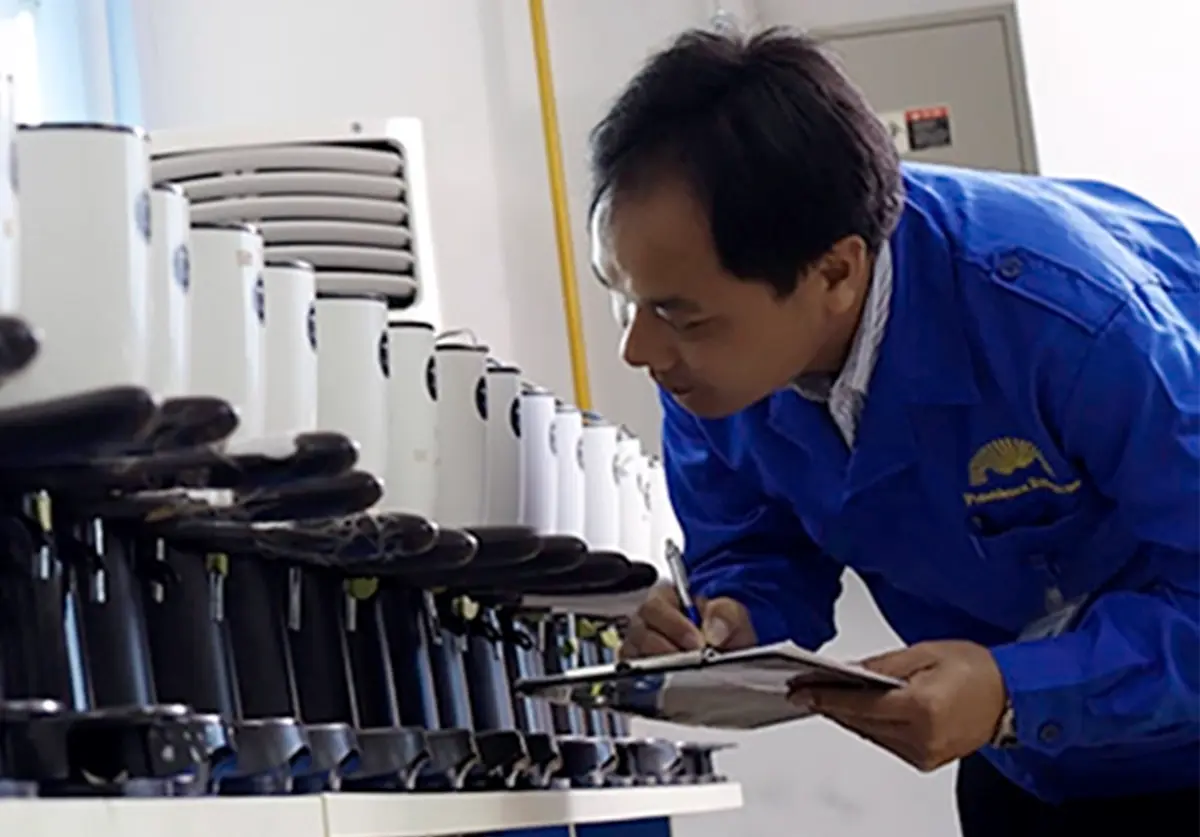
Beverage System Innovation
We're your go-to partner for developing and manufacturing beverage systems, turning your ideas into reality with quality and innovation.
View Detailed List
- Consumer & Commercial Systems: Food, Espresso, Coffee, Tea, & Water Appliances
- Connected Systems: WiFi, Bluetooth, Zigbee, Z-Wave, and RFID
Certified for Your Peace of Mind
Our certifications are a testament to our unwavering commitment to quality and compliance: ISO 27001, ISO 13485, ISO 14001, ISO 14971, ISO 9001, ISO 45001, IATF 16949, SA 8000, and FDA & NMPA registration.
View & Download Certifications ↓
|
|
|
|
|
|
|
|
|
|
Certified for Your Peace of Mind
Our certifications are a testament to our unwavering commitment to quality and compliance: ISO 27001, ISO 13485, ISO 14001, ISO 14971, ISO 9001, ISO 45001, IATF 16949, SA 8000, and FDA & NMPA registration.
View & Download Certifications ↓
|
|
|
|
|
|
|
|
|
|
Case Studies
-
Home Carbonated Beverage Appliance
-
Air Operated Diaphragm Pump
-
Pump with Electrostatic Isolation
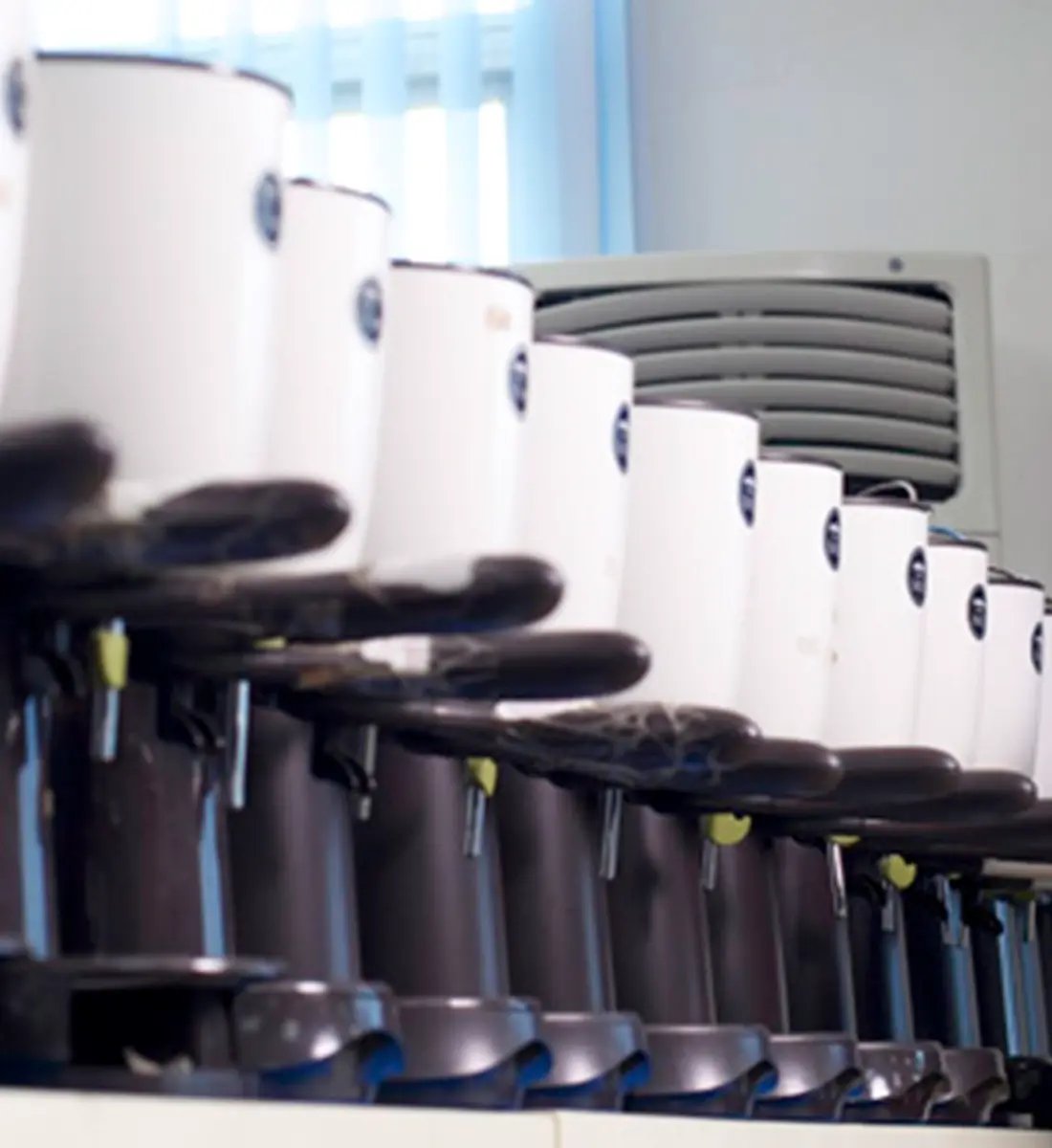
Beverage Appliance
Application: Home Carbonated Beverage Appliance
Challenge: Our client, the third largest beverage company in North America, had an aggressive market launch date of their temperature controlled, carbonated beverge appliance and only had a proof-of-concept prototype.
Goals: To cost effectively meet their deadlines and be production ready to produce 2 million units per year.
Solution: Providence leveraged its highly integrated supply chain to meet the demanding timeline. This included in-house mold making capabilities, partnering with developed suppliers, and utilizing our Research & Development team to support the customer. Additionally, we constructed a temperature-controlled testing environment to ensure consistent carbonation levels during production across all manufacturing bases.
Results: Despite encountering over 100 engineering changes throughout development and production, Providence successfully delivered the project on time.
Air Operated Diaphragm Pump Cost Reduction
Application: Air-operated diaphragm pump used in commercial beverage equipment.
Challenge: The client initiated a Green Belt project aimed at reducing the costs of a high-volume workhorse pump used in the beverage industry. The product had previously undergone multiple cost reduction exercises. To justify this project, a more aggressive approach to cost reduction was necessary.
Goals: The project required thorough qualifications from end-user customers due to the global installation footprint. An improperly executed cost reduction could result in service costs far exceeding the product's acquisition cost.
Solution: We redesigned the gear pump, developed a new Coreless DC motor to replace the original German motor, molded the internal gears with PEEK material to replace the original CNC Stainless Gears, and suggested cost-effective materials to help them achieve their cost target goals.
- Define: This Green Belt project necessitated innovative, out-of-the-box thinking to achieve cost reductions beyond the conservative measures previously implemented.
- Measure: The impact of cost reduction and the investment required for the engineering change were calculated, along with the payback period.
- Analyze: The product cost was meticulously analyzed down to each specific component. A Pareto analysis identified the primary cost drivers of the pump. A feasibility study was conducted to assess potential design changes.
- Implement: Two significant decisions were made:
- Change the pump material from acetal to polypropylene (PP) with an additional design change to include an insert-molded bearing.
- Reduce the shaft size and switch from standard O-rings to a lip seal system.
- Control: The pump underwent rigorous life tests and end-user field tests before global release. Periodic life tests were conducted every three months until confidence in the design changes was solidified after two years.
Results: This Green Belt project achieved record cost reductions in both dollar terms and percentage of product cost within the client’s division. Additionally, the changes to the pump's wetted parts materials improved chemical compatibility with all new beverage offerings.
Disinfectant Pump Development
Application: Sanitizer sprayer required a pump with electrostatic isolation to the electrical system due to an electrostatic spray nozzle that charges the liquid as it exits the sprayer nozzle.
Challenge: A market leader in the commercial sanitization sprayer industry approached us with the need for a pump that would address efficiency issues caused by electrostatic leakage and harsh chemicals. No standard pump manufacturer was able to supply a suitable pump. The pump needed to be developed on a very aggressive schedule due to the global pandemic.
Goals: Develop a positive displacement diaphragm pump with electrostatic isolation between the pump and motor. This pump also needed an enclosure to protect the motor from electrostatic impact in case of moisture inside the sprayer compartment.
Solution: We developed a pump solution featuring an isolation coupler between the pump and motor. The coupler, made of nonconductive material, isolated the electrostatic path between the fluid being pumped and the motor. Compression fittings and enclosures were incorporated into the pump design to reduce the total part count. Materials for the pump and diaphragm were chosen to ensure compatibility with the customer’s application.
Results: The pump met all performance requirements. It was designed and manufactured to meet the customer’s cost target and developed on a very aggressive schedule to meet the urgent need of the global pandemic.
When I was searching for a new contract manufacturer, it was easy to find tons of contract manufacturers that have certifications and documentation standards that live in a filing cabinet - but my question was, “Do they actually live it?” We’ve seen this to be the case with Providence - they deliver on their promises - they are who they say they are.
Michelle P., Senior Manager of Sourcing
at a Health & Wellness Products Company
When I was searching for a new contract manufacturer, it was easy to find tons of contract manufacturers that have certifications and documentation standards that live in a filing cabinet - but my question was, “Do they actually live it?” We’ve seen this to be the case with Providence - they deliver on their promises - they are who they say they are.
Michelle P., Senior Manager of Sourcing
at a Health & Wellness Products Company
The hassle-free way to manufacture your products with confidence.
![]()
|
Contact Usto discuss your project's unique needs. |
![]()
|
Get a tailored solutionwith a custom project proposal. |
![]()
|
Experienceour global industry standards with a factory tour. |
![]()
|
Discoverwhat it means to manufacture with confidence. |
The hassle-free way to manufacture your products with confidence.
![]()
|
Contact Usto discuss your project's unique needs. |
![]()
|
Get a tailored solutionwith a custom project proposal. |
![]()
|
Experienceour global industry standards with a factory tour. |
![]()
|
Discoverwhat it means to manufacture with confidence. |
Our Process
-
Planning
Discover the ease of working with us at every stage of manufacturing.
Learn More → -
Development
Experience seamless collaboration at every manufacturing stage with us.
Learn More → -
Verification
Unlock a hassle-free manufacturing experience with us every step of the way.
Learn More → -
Pre-Production
Simplify your manufacturing journey with us by your side at every stage.
Learn More → -
Production
Experience a smooth journey through all manufacturing stages with us.
Learn More →
Discover the ease of working with us at every stage of manufacturing.
Learn More →
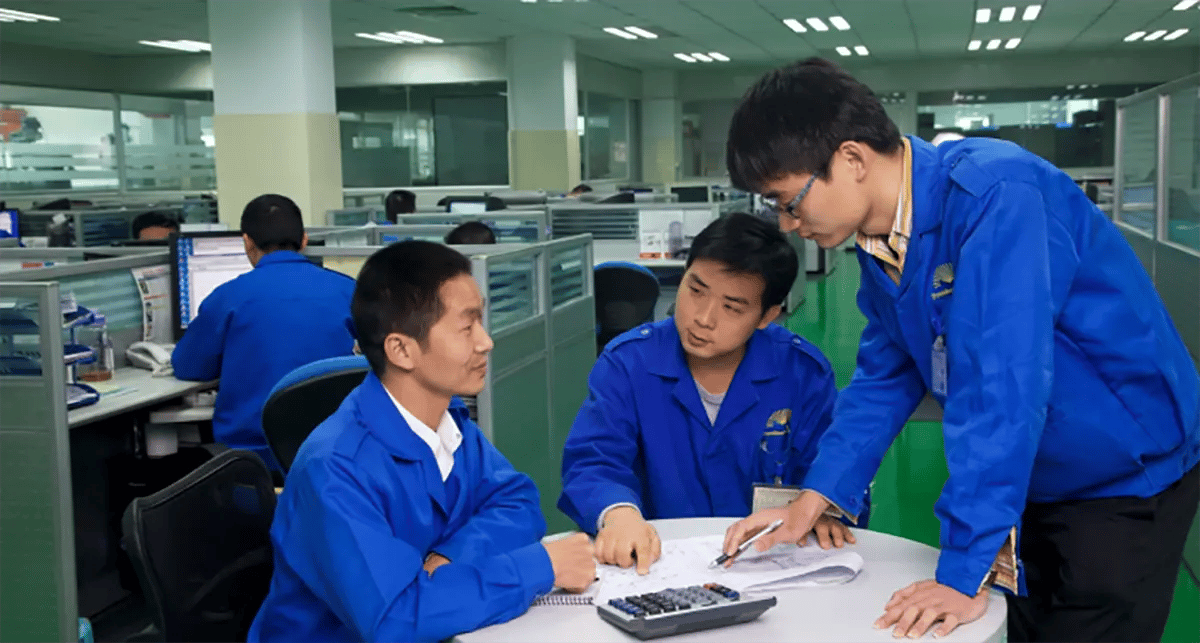
Planning
In the planning phase of our partnership, we take a comprehensive approach to understand your project requirements, goals, and timelines. Our team conducts thorough assessments to identify potential challenges and opportunities, allowing us to develop a customized plan that aligns with your vision. With clear communication and transparent collaboration, we ensure that every aspect of the planning process is meticulously addressed, setting the foundation for a successful project execution.
Experience seamless collaboration at every manufacturing stage with us.
Learn More →

Development
During the development phase of our collaboration, our team of engineering specialists brings your vision to life with precision and expertise. We leverage state-of-the-art technology and innovative methodologies to translate concepts into tangible products, while adhering to strict quality standards and regulatory requirements. Throughout this phase, we maintain open communication and provide regular updates, ensuring transparency and alignment with your project goals. Our commitment to excellence drives us to deliver optimal results and exceed expectations at every stage of development.
Unlock a hassle-free manufacturing experience with us every step of the way.
Learn More →
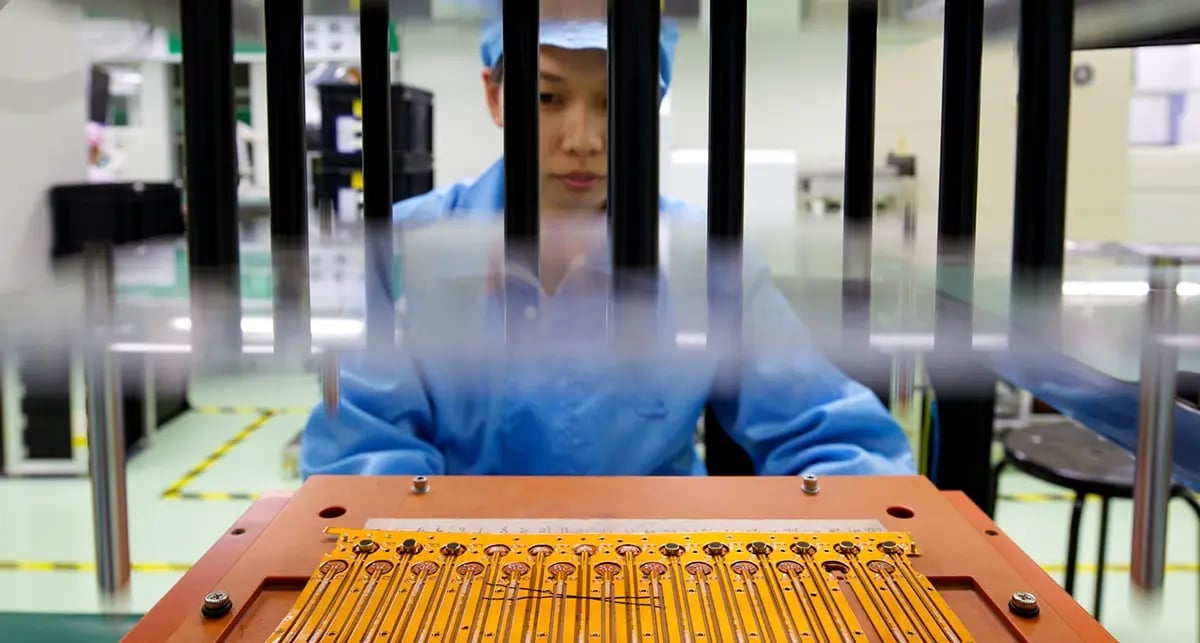
Verification
In the verification phase of our partnership, we meticulously test and validate every aspect of the product to ensure it meets the highest standards of quality and performance. Our team employs rigorous testing protocols and quality control measures to identify any potential issues and make necessary adjustments. With a focus on accuracy and precision, we verify that the product is ready for market launch, providing our clients with confidence in its reliability and effectiveness.
Simplify your manufacturing journey with us by your side at every stage.
Learn More →
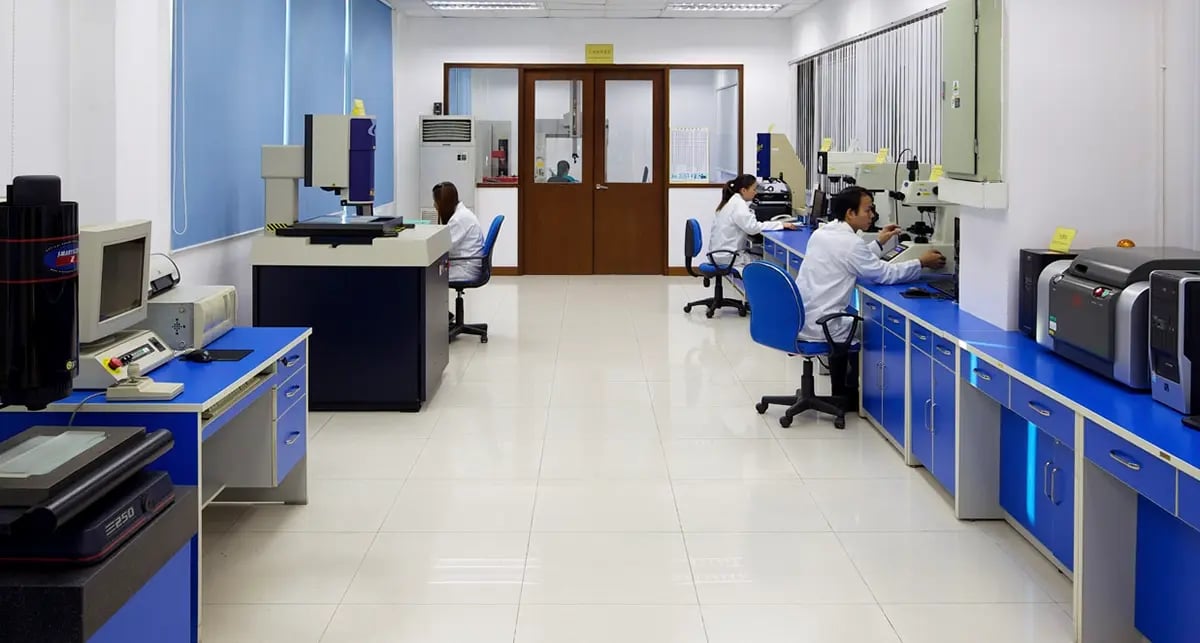
Pre-Production
In the pre-production phase, we meticulously prepare for manufacturing by fine-tuning processes and optimizing workflows to ensure efficiency and quality. Our team conducts thorough testing and validation of equipment and procedures to identify and address any potential issues before full-scale production begins. With a focus on precision and attention to detail, we lay the groundwork for a seamless production process, ultimately delivering high-quality products that meet or exceed our clients' expectations.
Experience a smooth journey through all manufacturing stages with us.
Learn More →
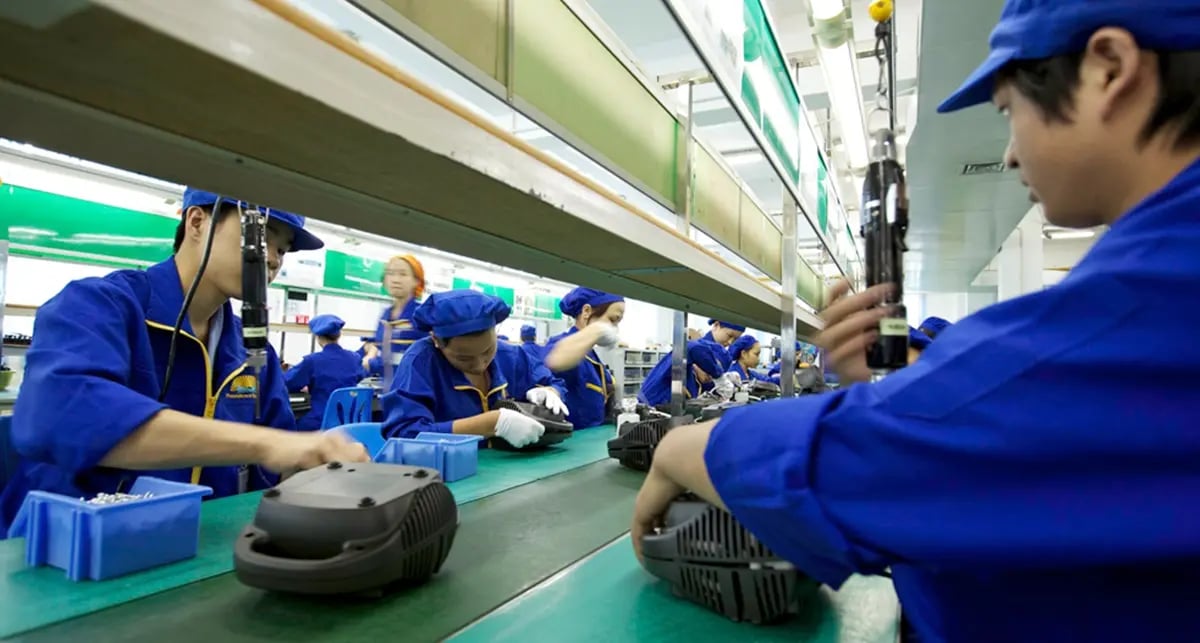
Production
During the production phase, our team executes the manufacturing process with precision and efficiency, leveraging state-of-the-art technology and industry-leading practices. We maintain strict quality control measures throughout the production process to ensure consistency and reliability in every product. With a commitment to meeting deadlines and exceeding expectations, we deliver high-quality products that meet the unique needs of our clients and their target markets.
FAQ
What type of projects do you typically work on?
We have been manufacturing beverage pumps since 1992. In addition to pumps, we also manufacture hot and cold beverage appliances and related systems that involve smart technologies, temperature control, carbonated, and non-carbonated features.
We are FDA QSR & 13485 compliant and have well-maintained Class 7 & 8 Cleanrooms. Our vertically integrated manufacturing capabilities enable us to work closely with our partners to ensure production is flexible, scalable, and yields high-performance results.
How can you help us control our costs?
Design transfer: How ready is your design for manufacturing? Some designs require more preparation for manufacturing than others. Rest assure, we guide you through this process as seamlessly as possible.
Materials and design preferences: Some companies and products require very specific materials and designs; Whereas others have a focus on performance, regardless of how it looks or what it’s made out of. Sometimes, using alternative materials, and adjusting the specific design, can help reduce your cost-per-product, without jeopardizing its performance.
Component technicality: Some products feature multiple systems that must work together. If your manufacturer is not accustomed to connecting multiple system together, the process can be challenging. Not to mention, you might still end up with a product that doesn’t work or is prohibitively expensive. Complexity does not intimidate us and electromechanical manufacturing is our specialty. We help our customers determine the most cost-effective way to bring their products to market, at scale, without jeopardizing performance.
Timeline: We have organized ourselves to be nimble. While your budget might not be as nimble, we can work with you to determine the best approach to render your compressed timeline a non-issue. For tight deadlines, we do offer an expedited approach which allows us to have multiple aspects of your project working in parallel, such as tooling, molding, SMT, and ordering materials simultaneously.
Volume and inventory: This is one of the hardest decisions many businesses have to make. You can lower your costs by ordering more, but how soon will all the units sell, and where do you store the influx in the meantime? Luckily, we have ways of helping our partners manage this process with safety stock, risk buys, and even expedited production. We can produce more units for you within two weeks if the materials are on-hand.
Ability to customize your manufacturing process: To automate, or not to automate, that is the question. Believe it or not, but it is possible to over- automate your manufacturing process. This could result in project delays and added costs. Conversely, a fully manual process doesn’t often work either, as it’s hard to maintain quality consistency, and costs can add up here as well. We help all our partners determine the correct amount of automation so that they don’t have to choose between quality consistency, speed of manufacturing, or their costs.
Testing efficiency and quality management: Mistakes cost money. This is why we have a rigorous process to test quickly and on a small scale. Our monitoring systems allow us to detect and immediately correct issues throughout the manufacturing process. This leads to an incredibly low failure rate of 0.05% which means your budget is utilized in the most efficient way possible.
With your different locations, how do you manage language barriers?
Different countries involve not only different languages, but different cultures. Sometimes it is not enough to simply have a translator. You need someone who can relate to the other organizations culture, to better understand the language. We have native representatives that can communicate with our clients regardless of where their locations may be. Our most common communication exchange is in English.
How do you maintain a high-degree of quality?
We collect data throughout the manufacturing process to monitor for issues and performance. Such data includes: Test Data, Batch Data via RFID or Barcode, Networked production lines, collect data on injection molding systems.
We have cameras set up to watch the entire process, especially for key areas which include molding, soldering, and assembly.
How soon can issues be detected, and corrected? Immediately! The constant supervision of the process allows us to act quickly, helping to preserve the timeline and budget.
What’s your rejection rate? Less than 500 defective parts per million; This results in producing very little scrap material and reducing costs.
How big are the batches that you test? We follow ISO and AQL standards.
We collect data throughout the manufacturing process to monitor for issues and performance. Such data includes: Test Data, Batch Data via RFID or Barcode, Networked Production Lines, and Injection Molding efficiency.
Do you require companies of a certain size to work with you?
Our mid-market size has positioned us perfectly to remain nimble for companies big and small, without jeopardizing our ability to deliver quality products consistently, scale to incredibly high-volume outputs, or impede our ability to help you control your costs.
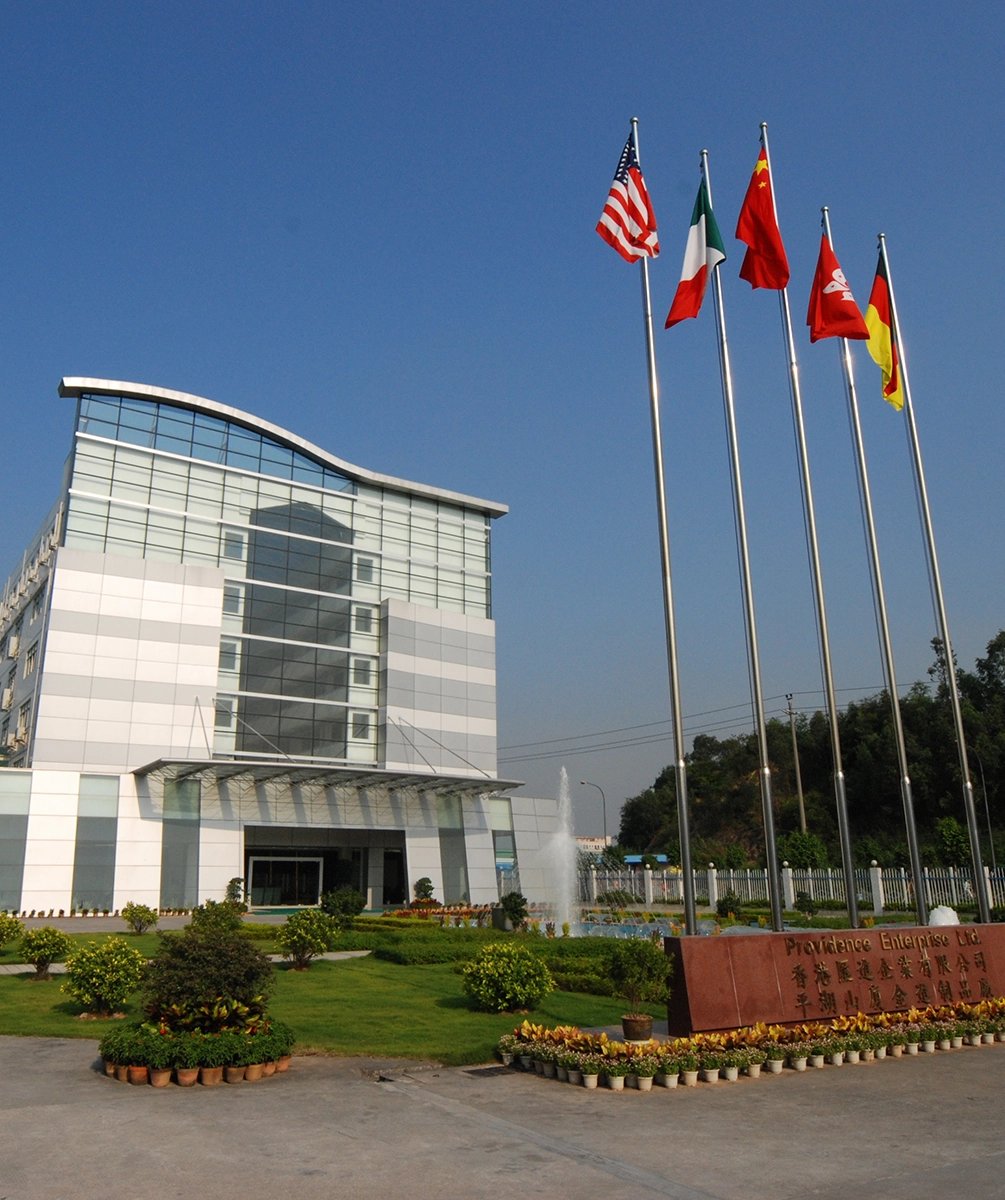
Want a Preview of What It’s Like to Work With Us?
Get an exclusive look into our factory, processes, and people, so you can manufacture your product with confidence.
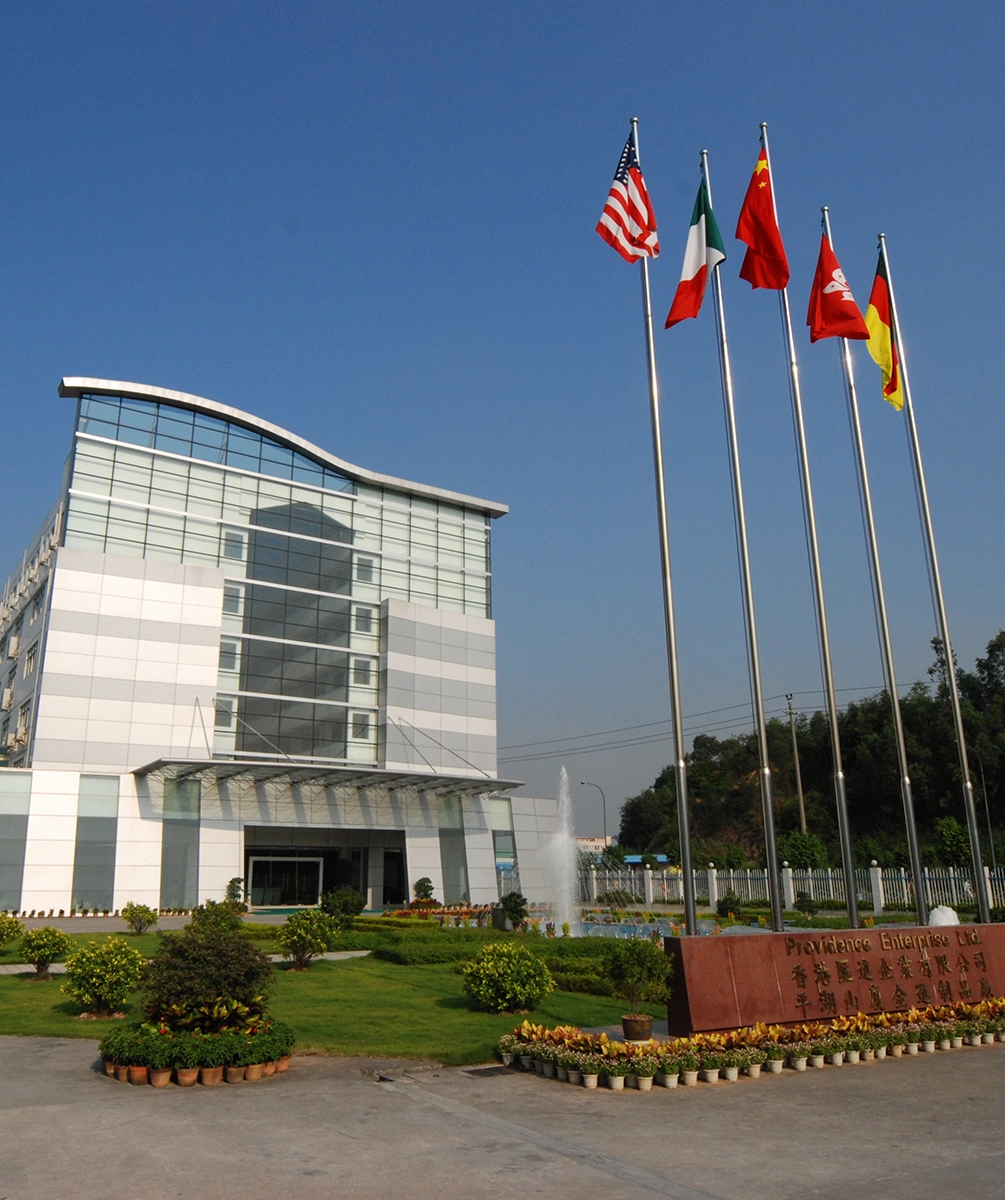
Want a Preview of What It’s Like to Work With Us?
Get an exclusive look into our factory, processes, and people, so you can manufacture your product with confidence.